Products & Services
List of products
Catalogs
Mixers
Small machines
Water treatment
Petrochemistry
Food & beverage
Medicines
Bio & regenerative medical techniques
Paints
Paper manufacturing
For experiments
Super-mix Series
Classifier
Bioreactors
Realization of Industrialization / Commercial Production / Scalability
Microbial culture
HSF ReactorAnimal cell culture
MRF ReactorAnimal cell culture
MRF-RB ReactorAnimal cell culture
VMF ReactorAnimal cell culture
VerSus ReactorRegenerative medicine
VMF-WSUB Reactor/TCSSingle-use BioReactor
iPS cell culture
HiD4×4Fittings/Options
Solutions
Development of exclusive mixers・
and impellers by purpose of useContracted numerical calculation
Evaluation of contracted cell culture
Classification performance evaluation
Environmental testing equipment
BioReactors
HSF Reactor
MRF Reactor
MRF-RB Reactor
VMF Reactor
VerSus Reactor
VMF-WSUB
Reactor/TCSSingleUse
BioReactorHiD4x4
Fittings/Options
VerSus Reactor
Collaboration of VMF Reactor/SPG membrane sparger
Development, Customization, and Single-use support of Exclusive Reactor in Accordance with Requirements Specifications
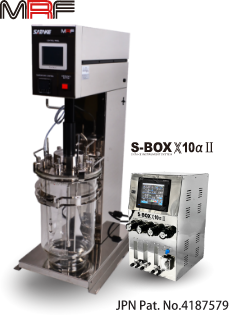
SPG membrane sparger
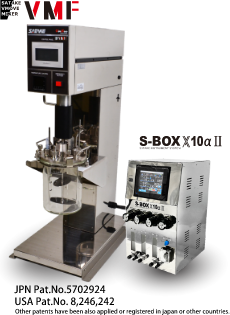
The micro-bubbles can be homogeneously dispersed inside the tank.
*SPG membrane sparger has been developed jointly by MIYAZAKI PREFECTURE INDUSTRIAL TECHNOLOGY CENTER and JGC Corporation.
We promise further improvement in production efficiency with the “VerSus Reactor” which is a collaboration of the “VMF Reactor” that controls the physical action in the cell culture tank and “SPG membrane sparger”, which is an excellent micro bubble technology.
■Culture example
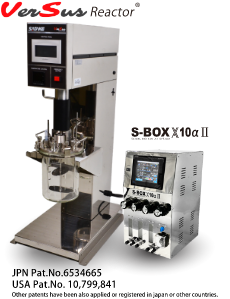
Comparison of cell viability
by CHO cells
The growth curve of CHO cells based on the presence of SPG membrane sparger is shown by using the VMF reactor. It is understood that the culture results improves significantly by using the SPG membrane sparger. Due to micro-bubbles having extremely high homogeneity, the high gas absorption performance significantly reduces the DO air flow rate, which is the cause of formation of a foam layer, without disturbing the weak flow. VerSus reactor has a significantly improved total performance.
Comparison of production of
antibodies by CHO cells
The result* of scale-up from the control quantity of 8 l to 150 l by using CHO cells having high dependability on the shear stress is shown below. Here, the actually commercially-available production of antibodies is undertaken. As a result, in the 150-l scale-up condition, either almost the same or more volume of production of antibodies than the control quantity of 8 l was obtained. This scale-up is performed by the numerical fluid calculation at a constant shear factor, and its advantage in the combined use of computational fluid dynamics and cell culture has been proved.
* The result of joint research with JGC Corporation
Item | Specifications | ||||
---|---|---|---|---|---|
Name | VerSus Reactor | ||||
Model | VSR-05 | VSR-1 | VSR-3 | VSR-10 | |
Temp. control device | Band heater (PID control) with over-temperature protection function (Max. 80 [℃]) | ||||
Power transmission | Linear shaft drive non-sealing type | ||||
Gas supply type | Shirasu porous glass (SPG) membrane type (additional option : sintered metal type) | ||||
Performance*1 | Temp. control range | Room temperature + 5 - 20 [℃] (normally set to 37 [℃]) | |||
Temp. accuracy | ±0.3 [℃] (37 [℃]) | ||||
Max. shaft stroke | 40 [mm] | ||||
Max. shaft speed | 300 [mm/s] | ||||
Function | Temp. setting | Touch panel input, data output DC1 - 5 [V] | |||
Vertical motion setting | Touch panel input, data output DC0 - 5 [V] | ||||
Configuration | Power of band heater | 60 [W] | 105 [W] | 160 [W] | 480 [W] |
Power of motor | Max. power 800 [W] | ||||
Mixing impellers | VM200 | VM100+VM200*2 | |||
Culture tank | Dimensions | I.D. 90 x Depth 200 [mm] | I.D. 110 x Depth 169 [mm] | I.D. 140 x Depth 203 [mm] | I.D. 200 x Depth 360 [mm] |
Culture operation volume | 0.3 [L] | 1.2 [L] | 2.4 [L] | 7 [L] | |
Usage condition | 10 - 35 [℃] | ||||
Outer dimensions | W360×D485×H905 [mm] | ||||
Weight | Approx. 28 [kg] | Approx. 28 [kg] | Approx. 30 [kg] | Approx. 34 [kg] | |
Power supply | AC100 [V], 50/60 [Hz] | ||||
*1 The performance is the value under room temperature 20 [℃], power supply AC100 [V], 50 [Hz] and no load condition. | |||||
*2 Depending on the Culture operation volume, the only mixing impeller may be only the VM200. |
Item | Specifications | |||||||||||
---|---|---|---|---|---|---|---|---|---|---|---|---|
Name | Culture controller | |||||||||||
Model | S-BOX×10αII | |||||||||||
Control | pH, DO (Dissolved oxygen), FL (O₂ flow rate), Pump | |||||||||||
Display range/accuracy | pH (Hydrogen ion concentration) | 0.00 - 14.00 [-] | Display accuracy: ±0.5 [%] F.S. | |||||||||
DO (Dissolved oxygen) | 0.00 - 20.00 [mg/L] | |||||||||||
FL (O2flow rate) | 0.00 - 20.00 [mL/min] | |||||||||||
Setting range | pH (Hydrogen ion concentration) | 0.00 - 14.00 [-] | ||||||||||
DO (Dissolved oxygen) | 0.00 - 10.00 [mg/L] | |||||||||||
FL (O2flow rate) | 0.00 - 20.00 [mL/min] | |||||||||||
Control type | pH (Hydrogen ion concentration) | ON/OFF control | ||||||||||
DO (Dissolved oxygen) | O2addition/subtraction step control | |||||||||||
O2and N2ON/OFF control | ||||||||||||
O2PI control (slope set method: TIME, %) | ||||||||||||
FL (O2flow rate) | PI control (slope set method: TIME, %) | |||||||||||
Data output | pH (Hydrogen ion concentration) | With data logger DC0 - 5 [V] (option : Load factor can be outputted.) |
Accuracy: ±0.5 [%] F.S. | |||||||||
DO (Dissolved oxygen) | ||||||||||||
FL (O2flow rate) | ||||||||||||
Mixing frequency | ||||||||||||
Temperature sensor | DC1 - 5 [V] | |||||||||||
MTA of outer surface | SUS304 (no coating), indoor type, non-waterproof, non-explosion proof specification | |||||||||||
Installation | Indoor tabletop type | |||||||||||
Outer dimensions/weight | W350×D400×H530 [mm] ・ Approx. 15 [kg] | |||||||||||
Usage conditions | Temperature | 5 - 45 [℃] | Humidity | 20 - 85 [%] RH (No condensation) | ||||||||
Sensors | Polarographic DO sensor/pH sensor manufactured by Mettler Toledo company | |||||||||||
(Option: Optical DO sensor manufactured by Automatic System Research Co., Ltd. ) | ||||||||||||
Utilities | Power supply | AC100 [V], 50/60 [Hz], electrical outlet 2 gang (for main control unit and recorder) | ||||||||||
N2 | Flow rate 50 [mL/min] or lower, supply pressure 0.2 [MPa], connection port φ6 one touch tube fitting | |||||||||||
O2 | Flow rate 20 [mL/min] or lower, supply pressure 0.2 [Mpa] connection port φ6 one touch tube fitting | |||||||||||
CO2 | Flow rate 50 [mL/min] or lower, supply pressure 0.2 [MPa], connection port φ6 one touch tube fitting | |||||||||||
AIR | Flow rate 150 [mL/min] or lower, supply pressure 0.2 [MPa], connection port φ6 one touch tube fitting | |||||||||||
*All of N2, O₂, CO₂, and AIR must be dry and clean gases that do not contain corrosive components, dust, and oil mist. |