Products & Services
List of products
Catalogs
Mixers
Small machines
Water treatment
Petrochemistry
Food & beverage
Medicines
Bio & regenerative medical techniques
Paints
Paper manufacturing
For experiments
Super-mix Series
Classifier
Bioreactors
Realization of Industrialization / Commercial Production / Scalability
Microbial culture
HSF ReactorAnimal cell culture
MRF ReactorAnimal cell culture
MRF-RB ReactorAnimal cell culture
VMF ReactorAnimal cell culture
VerSus ReactorRegenerative medicine
VMF-WSUB Reactor/TCSSingle-use BioReactor
iPS cell culture
HiD4×4Fittings/Options
Solutions
Development of exclusive mixers・
and impellers by purpose of useContracted numerical calculation
Evaluation of contracted cell culture
Classification performance evaluation
Environmental testing equipment
Classifier
SATAKE i Classifier
High-precision wet classifier equipped with our newly developed rotor
High-precision wet classifier capable of precision classification according to customer requirements
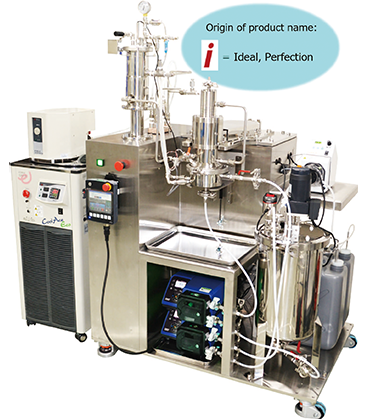
SATAKE i Classifier is equipped with a classifying rotor which rotates at high speed.
The classifying rotor has a classification blade to stabilize the centrifugal field.
■Flow path
When raw slurry is pumped into the classifier, some fluid passes between the blades of the rotor and goes inside the rotor.
Fine slurry passes through the hollow shaft and is discharged outside the machine.
Meanwhile, coarse slurry is discharged from the classifying rotor by centrifugal force and re-supplied as raw slurry.
■Classifying rotor
i Classifier's classifying rotor is designed with an optimal shape based on many classification tests and CFD flow analysis optimization so that the classification particle diameter is constant in the classification chamber. We succeeded in straightening the flow inside the classification chamber and the rotor, dramatically improving classification accuracy.
■Principle of classification

The particles at the outer end of the rotor are acted upon by the centrifugal force generated by the rotational motion of the fluid and the drag (buoyancy) caused by the radial movement of the particles.
There is a particle size "= classification particle diameter" where these external forces are exactly balanced.
Particles larger than the classification particle diameter (coarse particles) receive a large centrifugal force and cannot enter the rotor because they move outward. Particles smaller than the classification particle diameter (fine particles) can enter the rotor by riding on the liquid flow, and only these fine particles are recovered outside the machine as slurry.
■Throughput

The graph shows the throughput of the machine.
(Material: metal, SiO2, PMMA)
The throughput varies depending on the raw material and the desired classification size.
How to read the graph
(Example) When the 50% separation diameter is 2 (μm)
The slurry processing speed is:
PMMA particles: 1.2 (L/hr)
SiO2 particles: 8 (L/hr)
Metal particles: 50 (L/hr)
∗ When water is used as a dispersion medium
Please contact us about the throughput for raw materials other than the above.
Machine Specifications | ||||
---|---|---|---|---|
Item | i-Classifier「Standard model」 | i-Classifier「Laboratory model」 | ||
Dimension Weight | 890×1155×1652 Approx. 430kg |
Main unit | W200×D360×H600・20kg | |
Control box | W300×D330×H200・10kg | |||
Rotational speed | 666~6660rpm | 1000~10000rpm | ||
Classifier rotor tip speed | 3~30㎧ | Approx. 2~20㎧ | ||
Classifier particle size | 0.5~20μm | 0.5~20μm | ||
Treatment volume | Max 50L/hr,100L/hr | Max. 5L/h | ||
Classifier chamber volume | 0.4L | Approx. 50ml | ||
Wetted part material | Rotor | Any of the following (Depend on specs) SUS304/SUS316L/Resin |
Resin | |
Stator | Any of the following (Depend on specs) SUS304/SUS316L |
Any of the following SUS304/SUS316L |
||
O-ring | Any of the following (Depend on specs) FKM/FFKM |
FKM/FFKM | ||
Ferrule packing |
PTFE | FKM/FFKM | ||
Others | Any of the following (Depend on specs) SUS304/SUS316L |
Any of the following SUS304/SUS316L |
||
Shaft seal | Double mechanical seal | - | ||
Seal liquid | Water, Organic dispersant (Depend on specs) |
- |
Utility specifications | ||
---|---|---|
Item | i-Classifier「Standard model」 | i-Classifier「Laboratory model」 |
Power supply | AC200V, 3-phase, 50/60Hz | AC100V, Single phase, 50/60Hz |
Power | 2200W (Main unit only) 4000W (Full package) |
1000W |
Compress air / Nitrogen | High pressure 0.7MPa (Pressure vessel) |
- |
Cooling water | Normal pressure (20~Below 30℃, Above 2~3 L/min) |
Normal pressure (20~Below 30℃, Above 2~3 L/min) |
∗We are continually developing our products to improve classification and performance.
We will notify you when there are specification changes, etc.
Classification process example
①Silica fine particles (ρ: 2200 kg/m3) - Fine particle and coarse particle remove process using aqueous dispersion
[Aims]
1.5 μm or less removal and
4.5 μm or more removal
(1) Silica fine particles (density: 2200 kg/m3) - Aqueous dispersion Fine particle remove process
Fine particles adhering to the surface of the raw material are completely removed by the fine particle remove process.
(2) Silica fine particles (density: 2200 kg/m3) - Aqueous dispersion Coarse particle remove process
The coarse particle remove process after the fine particle remove process gives particles with high monodispersity.
Silica fine particles (ρ: 2200 kg/m3) - Aqueous dispersion Particle size distribution
② Acrylic fine particles (1200 kg/m3) - Aqueous dispersion Coarse particle remove process
The particle size distribution can be freely controlled by the rotor peripheral speed.
③ Barium titanate (6000 kg/m3) - Aqueous dispersion Coarse particle remove process
The coarse particle cut removes the coarse particles and the distribution has a mode diameter of about 0.6 μm.